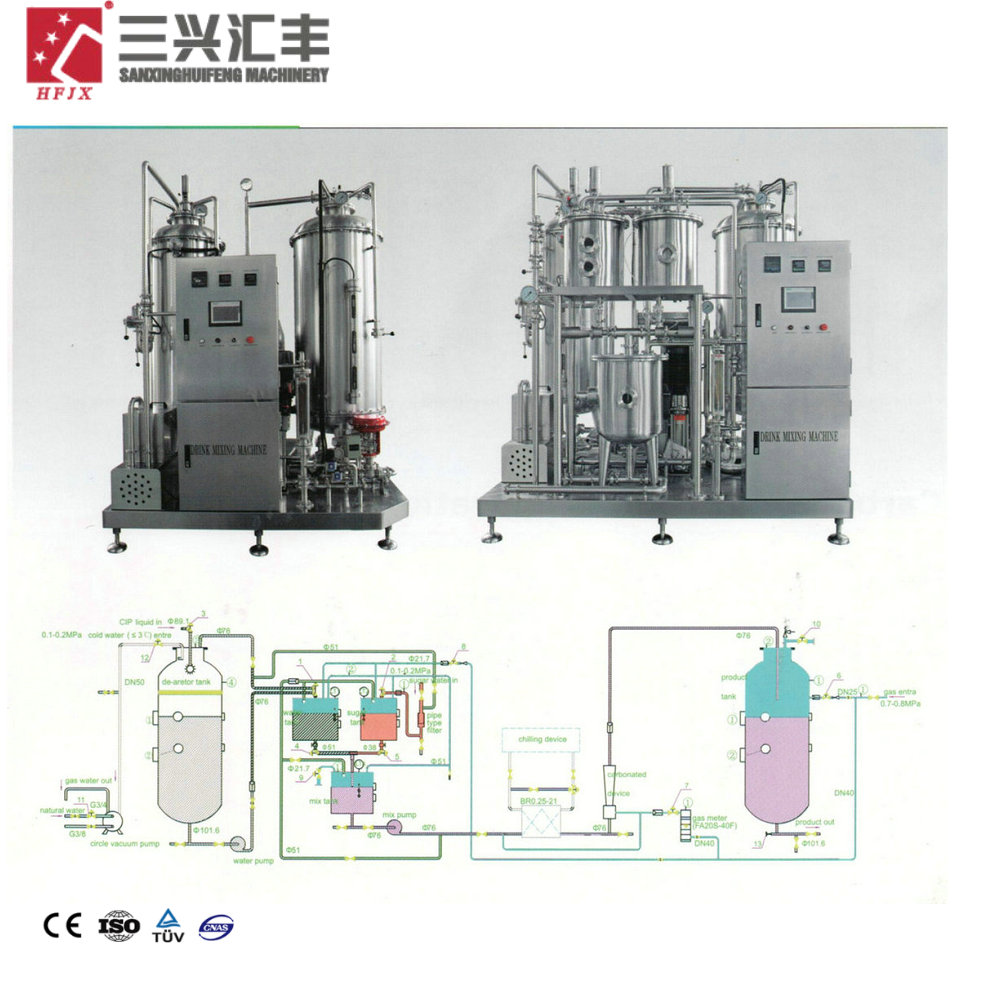
As carbonated drink mixer Manufacture ,we supply bottle blowing machine, filling capping labeling and packing machine

1) The carbonated drink mixer machine consists of vacuum deaeration unit, CO2 injecting device, CO2 counter-pressure device, cooling PHE, Product tank, automatic controlling device. The automatic controlling system includes pressure automatic control, water proportion automatic control, liquid level automatic control, carbonization automatic control, temperature automatic control and electric automatic control for the whole machine.
2) Operation principles: After deoxidized by vacuums system, the product water is output through pump and flow meter. After cooled water enters into the carbonation tank through mixing pump and control valve. Before entering into the tank, the mixing liquid is treated with pre-carbonization course. The CO2 content is controlled by flowrate control valve. At the moment the carbonation tank is charged with CO2 counter-pressure gas, and the sparkling water is stored in the bottom of the carbonation tank, and then pumped to the filler.
3) The flow meter blender is a real sense of automatic mixing. It has automatic control systems for mixing ratio, temperature, carbonization and pressure. With human-computer interface, operators can adjust the parameter values to change the CO2 content of the product. If there is any fault, it can stop and give an alarm automatically.
4) High efficiency deaeration system. After entering into the deaeration tank, the treated water has to be deoxidized to reduce the oxygen content in the water. It is helpful for CO2 dissolving in next carbonization process. Meanwhile, it can reduce the oxygen dissolving in the water to ensure the quality guarantee of the product.
5) Before water entering into the deaeration tank, CO2 is exchanged with the air in the deaeration tank. Water is sprayed in high speed into the tank through many little nozzles. The water appears misty and has bigger superficial area. It is helpful to extract the gas in the deaeration tank through water-seal vacuum pump.
6) Capacity adjustment system. With adjusting the opening-value of capacity adjusting valve, it is easy to adjust the production capacity.
7) High efficiency and accuracy carbonation. The CO2 gas volume can be adjusted stepless online within a certain range.
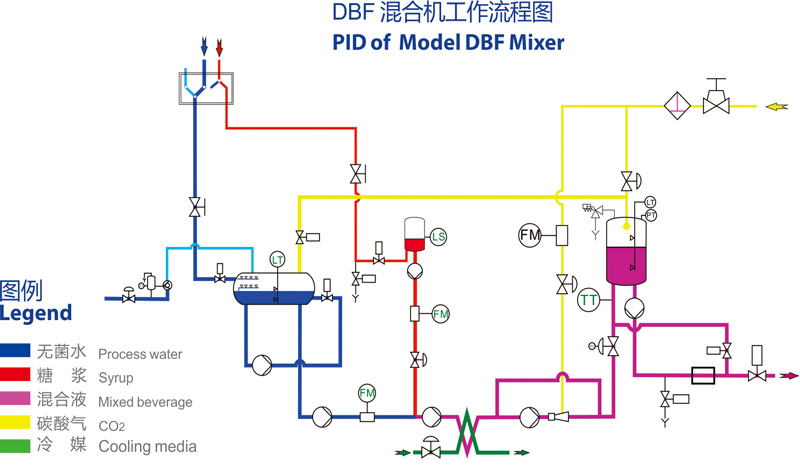
Main Parameter carbonated drink mixer
Series | DBF |
Capacity | Up to 15,000 liters per hour |
Mixing type | Electronic Flow meter |
Content of CO2 | 2.0~4.2GV |
Water supply pressure | 0.3~0.5 Mpa |
CO2 Supply pressure | 1.0~1.2 Mpa |
Syrup supply pressure | 0.2~0.4Mpa |
Compressed air supply pressure | 0.5~1 Mpa |
Consumption of compressed air | 6m3/h |
Glycol supply pressure | 0.2~0.3 Mpa |
Total installed power | 26.4kw |
Outer dimension | 4,600×3,200×3,100mm |
Net weight | 4,500kg |
Component Standard
PLC | Siemens |
HMI | Siemens |
Frequency Inverter | Danfoss |
Low voltage control parts | Siemens / Schneider |
Water pump | APV or Alfa Laval |
Mixing pump | APV or Alfa Laval |
Syrup pump | APV or Alfa Laval |
Product pump | Yuan’an |
Vacuum pump | SIHI |
PHE | Nanhua |
Water flow meter | E+H |
CO2 flow meter | E+H |
Syrup flow meter | E+H |
Capacity regulating valve | Samson |
Syrup regulating valve | Samson |
CO2 flow regulation valve | Samson |
Pneumatic parts | SMC |