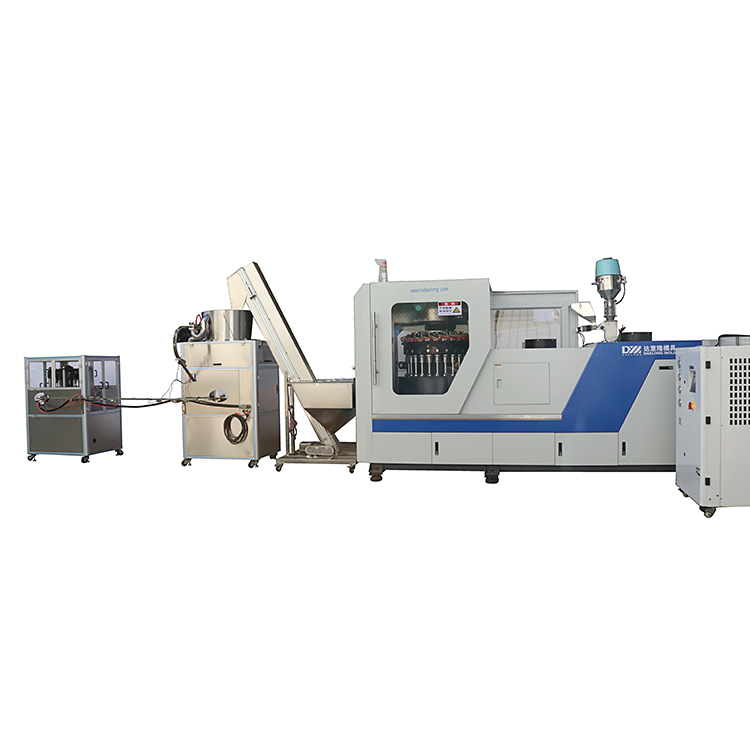
Product Description
18 Cavities Cap Compression Machine:
18 Cavities Cap Compression Machine Made in China can be bought with Low Price from Daelong, which is a professional high quality Cap Compression Machine Manufacturers and Factory in China. We provide Customized Products service. If you want Pricelist and Quotation, you can ask us by leaving a message. We will get back to you as soon as possible.
The Cap COMPRESSION MACHINE ADVANTAGES:
Shorter cycle time for higher productivity
Less energy consumption
High specific density
Maintenance-free molds that last decades
Quick colour changeover process
Less waste means lower costs
Technical Parameter
Model | DRCM-018 |
Production Capacity | 17000-18000/ hour (29/25MM cap) |
Cap Diameter | 20-45mm |
Cap Height | 10-30mm |
Cap Material | PP/HDPE/LDPE |
Mold Cavity No. | 18 |
Power | 380V/PH/50HZ |
Installation Power | 30KW |
Air Consumption | 0.3M3/Hr, 0.8Mpa |
Machine Dimension | 2660*1200*2000mm |
Machine Weight | 3.1T |
How the cap produced by the cap compression machine :




Why we choose the cap compression machine to produce the caps instead of the Injection molding machine:
COMPARED WITH INJECTION MOLDING MACHINE
Item | Cap compression molding machine | Injection molding machine |
Number of cavity | 24 | 2*24 |
Output | 16800-23400 | 2*6000 |
Power consumption | 26 | 2*36 (with mould) |
Power consumption per month | 18720 | 51840 |
Power save per month | 33120kw | |
Cost saving | $6650 00/month (if $0 2/kw/h) | |
Using additive | No | Yes |
Using mold release | No | Yes |
Peculiar smell | No | Yes |
Product appearance | No injection point | With injection point |
Waste | No | Yes |
Manpower resource | 1 | 2 or more |

EN SHORTER CYCLE time and therefore higher productivity. The lower extrusion temperature allows the cap to be cooled in the mould more quickly: this has shortened cycle times, which have, in the case of lightweight caps, been cut to around 2 seconds.
LESS ENERGY CONSUMPTION. Lower extrusion temperatures mean less energy is needed to bring the plastic to extrusion temperature and, since the plastic is colder, less energy to cool it is needed. Overall energy savings per cap produced can be as high as 45%.
HIGH SPECIFIC DENSITY. Moulding pressure being equal, lower temperatures allow attainment of a higher specific density; moreover, the injection point, which puts added strain on the molten plastic, is absent. This technological condition provides mechanical properties and a consistency that would be unattainable with injection.
CONSISTENCY has become a major issue in beverage bottling where production lines are ever-faster and more sophisticated and where cap-related plant stoppages can no longer be tolerated.
MAINTENANCE-FREE MOULDS that last decades. The vertical and axial movement of the compression mould ensures – unlike the injection mould, burdened by its own weight – that the moulds are protected from all kinds of wear. Compression moulding means no wear on the moulds for their entire working lives.
QUICK COLOR CHANGEOVERS These can be completed quickly without having to clean a hot chamber, which is absent in the compression process. LESS WASTE lower costs.

Machine Mould Detail List
Mould Material | Cavity | DC53, Japan |
Cavity Base | Beryllium Copper,USA | |
Cavity Pedestal | S136 .Sweden | |
Screw of Cavity Pedestal | DC53, Japan | |
Core | Beryllium Copper,USA | |
Thread Part | DC53, Japan | |
Medium Sleeve | DC53, Japan | |
De-moulding Sleeve | S136 .Sweden | |
Mould Hardness | After vacuum igniting, -180°C cryogenic treatment, nitriding, then DLC(Diamond-Like Carbon), the mould hardness is around 70 degree. |